- Faserverbundtechnologie
Fertigungstechnologien für Faserverbundkunststoffe - Additive Fertigungsverfahren
Additive Fertigung am IFB - Sandwichstrukturen
Sandwichbauteile und Faltwabenkerne - Digitalisierung von Produktionssystemen
FlexiCAM
Publikationen
Journals, Zeitschriften und Bücher
2025
- Kusoglu, Ihsan Murat, Sunidhi Garg, Arvid Abel, Prasanna V. Balachandran, Stephan Barcikowski, Louis Becker, Jan-Simeon Bernsmann, u. a. 2025. Large--Scale Interlaboratory Study Along the Entire Process Chain of Laser Powder Bed Fusion: Bridging Variability, Standards, and Optimization across Metals and Polymers. Advanced Engineering Materials (Juni). doi:10.1002/adem.202402930, .
- Dutta, G. S., M. Feyrer, G. Ziegmann, J. Bauer, S. Carosella, P. Middendorf, G. Oehl und J. Guhathakurta. 2025. Zero-waste prepreg production through the combination of automated fiber Placement and Online-Prepreg Technology: Tagungsband 6. Symposium Materialtechnik: 20. bis 21. Februar 2025 (Februar). doi:10.21268/20250506-2, .
2024
- Carosella, Stefan, Sebastian Hügle, Florian Helber und Peter Middendorf. 2024. A short review on recent advances in automated fiber placement and filament winding technologies. Composites Part B: Engineering 287 (Dezember): 111843. doi:10.1016/j.compositesb.2024.111843, http://dx.doi.org/10.1016/j.compositesb.2024.111843.
- Grisin, Benjamin, Stefan Carosella und Peter Middendorf. 2024. Vacuum Chamber Infusion for Fiber-Reinforced Composites. Polymers 16 (September). doi:10.3390/polym16192763, .
- Take, Jens. 2024. Die richtige Wellenlänge, The right wavelength. CUreports (Februar): 62–63.
- Kannenberg, Fabian, Christoph Zechmeister, Marta Gil Pérez, Yanan Guo, Xiliu Yang, David Forster, Sebastian Hügle, u. a. 2024. Toward reciprocal feedback between computational design, engineering, and fabrication to co-design coreless filament-wound structures. Journal of Computational Design and Engineering 11: 374–394. doi:10.1093/jcde/qwae048, .
2023
- Heudorfer, Klaus, Johannes Bauer, Yavuz Caydamli, Bruno Gompf, Jens Take, Michael R. Buchmeiser und Peter Middendorf. 2023. Method of Manufacturing Structural, Optically Transparent Glass Fiber-Reinforced Polymers (tGFRP) Using Infusion Techniques with Epoxy Resin Systems and E-Glass Fabrics. Polymers 15 (Mai). doi:10.3390/polym15092183, .
- Ackermann, Annika C., Martin Demleitner, Jajnabalkya Guhathakurta, Stefan Carosella, Holger Ruckdäschel, Sven Simon, Bronwyn L. Fox und Peter Middendorf. 2023. Mechanical, thermal, and electrical properties of amine-- and non--functionalized reduced graphene oxide/epoxy carbon fiber--reinforced polymers. Polymer Composites 44 (Mai): 4937–4954. doi:10.1002/pc.27461, .
- Rath, Amrita, Benjamin Grisin, Tarkes Dora Pallicity, Lukas Glaser, Jajnabalkya Guhathakurta, Nina Oehlsen, Sven Simon, Stefan Carosella, Peter Middendorf und Linus Stegbauer. 2023. Fabrication of chitosan-flax composites with differing molecular weights and its effect on mechanical properties. Composites Science and Technology 235 (April): 109952. doi:10.1016/j.compscitech.2023.109952, .
- Helber, Florian, Stefan Carosella und Peter Middendorf. 2023. Effects of reactive and non-reactive tackifying agents on mechanical neat resin and composite performance for preforming processes and Liquid Resin Infusion (LRI) techniques. Advanced Manufacturing: Polymer & Composites Science 9 (April). doi:10.1080/20550340.2023.2205796, .
- Take, Jens. 2023. UV-Aushärtung von Faserverbundbauteilen für den Mobilitätssektor, UV-curing of fiber composite componets for the mobility sector. CUreports (Januar): 70–71.
2022
- CU BW. 2022. Flugzeugbau trifft Architektur - TFP ermöglicht maßgeschneiderte Bio Composite Strukturen für die Architektur. Composite United 2022 (Dezember): 40–41. https://composites-united.com/flugzeugbau-trifft-architektur-tfp-ermoeglicht-massgeschneiderte-bio-composite-strukturen-fuer-die-architektur/.
- Helber, Florian, Stefan Carosella und Peter Middendorf. 2022. Quantitative Assessment of Reactive and Non-Reactive Binder Systems on First Ply Adhesion for Dry Fiber Placement Processes. Key Engineering Materials 926 (Juli): 1317–1326. doi:10.4028/p-5j966g, .
- Ackermann, Annika C., Michael Fischer, Alexander Wick, Stefan Carosella, Bronwyn L. Fox und Peter Middendorf. 2022. Mechanical, Thermal and Electrical Properties of Epoxy Nanocomposites with Amine-Functionalized Reduced Graphene Oxide via Plasma Treatment. Journal of Composites Science 6 (Mai): 153. doi:10.3390/jcs6060153, .
- Baranowski, Michael, Markus Netzer, Philipp Gönnheimer, Sven Coutandin, Jürgen Fleischer, Tristan Schlotthauer und Peter Middendorf. 2022. Functional Integration of Subcomponents for Hybridization of Fused Filament Fabrication. International Journal of Mechanical Engineering and Robotics Research (Januar): 319–325. doi:10.18178/ijmerr.11.5.319-325, .
2021
- Schlotthauer, Tristan und Peter Middendorf. 2021. Hollow stereolithographic structures reinforced by short carbon fibres. In: JEC Composite Magazine, 143:21–24. November.
- Grisin, Benjamin, Stefan Carosella und Peter Middendorf. 2021. Dry Fibre Placement: The Influence of Process Parameters on Mechanical Laminate Properties and Infusion Behaviour. Polymers 13 (Oktober). doi:10.3390/polym13213853, https://www.mdpi.com/2073-4360/13/21/3853.
- Caydamli, Yavuz, Klaus Heudorfer, Jens Take, Filip Podjaski, Peter Middendorf und Michael R. Buchmeiser. 2021. Transparent Fiber-Reinforced Composites Based on a Thermoset Resin Using Liquid Composite Molding (LCM) Techniques. Materials (Basel, Switzerland) 14 (Oktober). doi:10.3390/ma14206087, .
- Ackermann, Annika C., Stefan Carosella, Markus Rettenmayr, Bronwyn L. Fox und Peter Middendorf. 2021. Rheology, dispersion, and cure kinetics of epoxy filled with amine-- and non--functionalized reduced graphene oxide for composite manufacturing. Journal of Applied Polymer Science 139 (September): 51664. doi:10.1002/app.51664, .
- Lux, Benedikt, Julian Fial, Olivia Schmidt, Stefan Carosella, Peter Middendorf und Bronwyn Fox. 2021. Development of a shear forming envelope for carbon fibre non-crimp fabrics. Journal of Industrial Textiles (Juni). doi:10.1177/15280837211015470, .
- Berking, Tim, Sabrina G. Lorenz, Alexander B. Ulrich, Joachim Greiner, Eric Kervio, Jennifer Bremer, Christina Wege, Tatjana Kleinow und Clemens Richert. 2021. The Effect of Pooling on the Detection of the Nucleocapsid Protein of SARS-CoV-2 with Rapid Antigen Tests. Diagnostics 11 (Juni). doi:10.3390/diagnostics11071290, https://www.mdpi.com/2075-4418/11/7/1290.
- Facciotto, Silvio, Pavel Simacek, Suresh G. Advani und Peter Middendorf. 2021. Modeling of anisotropic dual scale flow in RTM using the finite elements method. Composites Part B: Engineering 214: 108735. doi:10.1016/j.compositesb.2021.108735, .
- Schlotthauer, Tristan, Jan Nitsche und Peter Middendorf. 2021. Evaluation of UV post-curing depth for homogenous cross-linking of stereolithography parts. Rapid Prototyping Journal ahead-of-print: 149. doi:10.1108/RPJ-12-2020-0309, .
- Schlotthauer, Tristan, Darren Nolan und Peter Middendorf. 2021. Influence of short carbon and glass fibers on the curing behavior and accuracy of photopolymers used in stereolithography. Additive Manufacturing 42: 102005. doi:10.1016/j.addma.2021.102005, https://www.sciencedirect.com/science/article/pii/S2214860421001706.
- Yong, A. X. H., A. Aktas, D. May, A. Endruweit, S. Advani, P. Hubert, S. G. Abaimov, u. a. 2021. Out-of-plane permeability measurement for reinforcement textiles: A benchmark exercise. Composites Part A: Applied Science and Manufacturing 148: 106480. doi:10.1016/j.compositesa.2021.106480, https://www.sciencedirect.com/science/article/pii/S1359835X21002025.
- Yong, A.X.H., A. Aktas, D. May, A. Endruweit, S. V. Lomov, S. Advani, P. Hubert, u. a. 2021. Experimental characterisation of textile compaction response: A benchmark exercise. Composites Part A: Applied Science and Manufacturing 142: 106243. doi:10.1016/j.compositesa.2020.106243, .
2020
- Sippach, Timo, Hanaa Dahy, Kai Uhlig, Benjamin Grisin, Stefan Carosella und Peter Middendorf. 2020. Structural Optimization through Biomimetic-Inspired Material-Specific Application of Plant-Based Natural Fiber-Reinforced Polymer Composites (NFRP) for Future Sustainable Lightweight Architecture. Polymers 12 (Dezember). doi:10.3390/polym12123048, .
- Engelfried, Mathias, Benedikt Aichele und Peter Middendorf. 2020. Investigation of the Friction between Dry and Wetted Carbon Filaments. Procedia Manufacturing 47: 60–64. doi:10.1016/j.promfg.2020.04.130, .
- Rihaczek, Gabriel, Maximilian Klammer, Okan Basnak, Jan Petrs, Benjamin Grisin, Hanaa Dahy, Stefan Carosella und Peter Middendorf. 2020. Curved Foldable Tailored Fiber Reinforcements for Moldless Customized Bio-Composite Structures. Proof of Concept: Biomimetic NFRP Stools. Polymers 12. doi:10.3390/polym12092000, .
- Zink, Dennis, Maximilian Huber und Peter Middendorf. 2020. FormPATCH - Forming of Complex Composite Structures using Patching Technologies. Procedia Manufacturing 47: 100–106. doi:10.1016/j.promfg.2020.04.143, .
- Czichos, Ruben, Oscar Bareiro, Anthony K. Pickett, Peter Middendorf und Thomas Gries. 2020. Experimental and numerical studies of process variabilities in biaxial carbon fiber braids. International Journal of Material Forming. doi:10.1007/s12289-020-01541-4, .
2019
- Raichle, A., Florian Ritter, M. Vinot, J. Dittmann, F. Fritz, L. Ott, C. Liebold, u. a. 2019. Weiterentwicklung des Digitalen Prototyps zum Digitalen Fingerabdruck. ATZ-Magazin 03/2019 (März).
- Harder, Nadine, Yves Klett, Sumee Park, Philip Leistner und Peter Middendorf. 2019. Bauphysikalische Untersuchung von Sandwichelementen. Bauphysik 41: 314–323. doi:10.1002/bapi.201900025, .
- Pickett, Anthony K. 2019. Process and mechanical modelling of engineering composites. Stuttgart: IFB (Institute of Aircraft design).
- May, D., A. Aktas, S. G. Advani, D. C. Berg, A. Endruweit, E. Fauster, S. V. Lomov, u. a. 2019. In-Plane Permeability Characterization of Engineering Textiles Based On Radial Flow Experiments: A Benchmark Exercise. Composites Part A: Applied Science and Manufacturing. doi:10.1016/j.compositesa.2019.03.006, .
- Klett, Yves, Fabian Muhs und Peter Middendorf. 2019. Analysis of Static and Dynamic Behavior of Thick-Walled PALEO Elements. In: Volume 5B: 43rd Mechanisms. doi:10.1115/DETC2019-97155, .
- Pickett, Anthony K. 2019. Introduction to Process and Mechanical Modelling of Engineering Composites. Stuttgart: IFB (Institute of Aircraft design).
- Carosella, Stefan, Dietmar Dieterle, Bettina Schrick, Josef Gaiser und Martin Hoffmann. 2019. Neue Wege des Faserlegens. Kunststoffe.
- Dittmann, Jörg und Peter Middendorf. 2019. Der digitale Prototyp: Ganzheitlicher digitaler Prototyp im Leichtbau für die Großserienproduktion. 1st ed. 2019. ARENA2036. https://doi.org/10.1007/978-3-662-58957-1.
- Fernández, Daniel, Benjamin Begemann, Peter Middendorf und Peter Horst. 2019. Investigation of the buckling and load-bearing behaviour of selectively stitched stiffened CFRP panels under multiaxial loading. CEAS Aeronautical Journal 10: 703–717. doi:10.1007/s13272-018-0343-y, .
- McGarrigle, Cormac, Daniel Fernández, Peter Middendorf, Thomas Dooher, John Kelly, Alistair McIlhagger, Eileen Harkin-Jones und Edward Archer. 2019. Extruded high-temperature thermoplastic tufting yarns for enhanced mechanical properties of composites. Journal of Reinforced Plastics and Composites 24: 073168441988636. doi:10.1177/0731684419886368, .
2018
- Muhs, Fabian, Yves Klett und Peter Middendorf. 2018. Automated numerical process chain for the design of folded sandwich cores. In: Origiami 7. August.
- Grzeschik, Marc, Yves Klett und Peter Middendorf. 2018. Reality Check - Mechanical Potential of Tessellation-based Foldcore Materials. In: Origiami 7. August.
- Helber, F., A. Amann, S. Carosella und P. Middendorf. 2018. Intrinsic fibre heating: a novel approach for automated dry fibre placement. IOP Conference Series: Materials Science and Engineering 406: 12064. doi:10.1088/1757-899X/406/1/012064, .
- Wellekötter, J., S. Baz, Johannes Schwingel, C. Bonten, Götz Theo Gresser und P. Middendorf. 2018. Kohlenstofffasern im Kreislauf halten. Kunststoffe 9.
- Kraemer, Matthias, Thomas Dauser, Peter Middendorf und Thomas Bauernhansl. 2018. Correlation between subjective perception and objective parameters for the characterisation of fibre print-through on surfaces of class A carbon fibre reinforced plastics via multidimensional scaling. Composites Part A: Applied Science and Manufacturing 115: 166–174. doi:10.1016/j.compositesa.2018.09.025, .
- Middendorf, Peter, Patrick Böhler, Florian Gnädinger, Frieder Heieck und Karin Birkefeld. 2018. 8.3 Design Study for a Carbon Composite Manipulator. In: Comprehensive Composite Materials II, 47–60. Elsevier. doi:10.1016/B978-0-12-803581-8.10048-7, .
- Bauer, Felix, Manuel Kempf, Frank Weiland und Peter Middendorf. 2018. Structure-property relationships of basalt fibers for high performance applications. Composites Part B: Engineering 145: 121–128. doi:10.1016/j.compositesb.2018.03.028, .
2017
- Heidenreich, Bernhard, Dietmar Koch, Harald Kraft und Yves Klett. 2017. C/C--SiC sandwich structures manufactured via liquid silicon infiltration. Journal of Materials Research 32 (September): 3383–3393. doi:10.1557/jmr.2017.208, .
- Fox, Bronwyn, Robert Bjekovic, Michael Elwert, Peter Middendorf, Florian Ritter, Christian Döbel, Claus-Christian Oetting, Klaus Fürderer, Maximilian Hardt und Dominik Rohrmus. 2017. Smarte Kunststoff-Bauteile für Automotive Innovation und Industrie 4.0. ZWF Zeitschrift für wirtschaftlichen Fabrikbetrieb 112: 522–525. doi:10.3139/104.111764, .
- Falk, G. und M. Blandl. 2017. Mach es aus Kunststoff -- Neues, recyclingfähiges Kunststoff-Werkzeugsystem für die Fertigung in der Großserie. Carbon Composites Magazin ISSN 2366-8024.
- Heieck, Frieder, F. Hermann, Peter Middendorf und K. Schladitz. 2017. Influence of the cover factor of 2D biaxial and triaxial braided carbon composites on their in-plane mechanical properties. Composite Structures 163: 114–122. doi:10.1016/j.compstruct.2016.12.025, .
- Szcesny, Marko, Frieder Heieck, Stefan Carosella, Peter Middendorf, Harald Sehrschön und Michael Schneiderbauer. 2017. The advanced ply placement process -- an innovative direct 3D placement technology for plies and tapes. Advanced Manufacturing: Polymer & Composites Science 3: 2–9. doi:10.1080/20550340.2017.1291398, .
2016
- Gnädinger, Florian, Peter Middendorf und Bronwyn Fox. 2016. Interfacial shear strength studies of experimental carbon fibres, novel thermosetting polyurethane and epoxy matrices and bespoke sizing agents. Composites Science and Technology 133: 104–110. doi:10.1016/j.compscitech.2016.07.029, .
- Klett, Yves und Peter Middendorf. 2016. Kinematic Analysis of Congruent Multilayer Tessellations. Journal of Mechanisms and Robotics 8: 34501. doi:10.1115/1.4032203, .
- Mallach, A., Frank Härtel, Frieder Heieck, Jan-Philipp Fuhr, Peter Middendorf und M. Gude. 2016. Experimental comparison of a macroscopic draping simulation for dry non-crimp fabric preforming on a complex geometry by means of optical measurement. Journal of Composite Materials. doi:10.1177/0021998316670477, .
- Finkenwerder, F. A., M. Geistbeck und Peter Middendorf. 2016. Study on the validation of ring filament winding methods for unidirectional preform ply manufacturing. Advanced Manufacturing: Polymer & Composites Science 2: 103–116. doi:10.1080/20550340.2016.1262090, .
- Bulat, Martina, Holger Ahlborn, Florian Gnädinger und D. Michaelis. 2016. Braided carbon fiber composites. In: Advances in Braiding Technology, 383–394. Elsevier. doi:10.1016/B978-0-08-100407-4.00015-6, .
- Heieck, Frieder, Stefan Carosella und Stefan Zuleger. 2016. Exemplary manufacturing process of a braided manipulator in serial production. In: Advances in Braiding Technology, 395–404. Elsevier. doi:10.1016/B978-0-08-100407-4.00016-8, .
- Nezami, Farbod, Jan-Philipp Fuhr, Diego Schierle, Chokri Cherif und Peter Middendorf. 2016. Hochqualitative CFK-Umformteile durch synchrone Bauteil- und Prozessentwicklung. Lightweight Design 9: 52–58. doi:10.1007/s35725-016-0012-1, .
2015
- Sturm, R. und Frieder Heieck. 2015. Energy absorption capacity of braided frames under bending loads. Composite Structures 134: 957–965. doi:10.1016/j.compstruct.2015.09.008, .
- Böhler, Patrick, Stefan Carosella, Christopher Goetz und Peter Middendorf. 2015. Path Definition for Tailored Fiber Placement Structures Using Numerical Reverse Draping Approach. Key Engineering Materials 651-653: 446–451. doi:10.4028/www.scientific.net/KEM.651-653.446, .
- Klett, Yves. 2015. Folding perspectives: Joys and uses of 3D anamorphic origami. In: Origami\^6, hg. von Koryo Miura. American Mathematical Society.
- Klett, Yves, Marc Grzeschik und Peter Middendorf. 2015. Comparison of compressive properties of periodic non-flat tessellations. In: Origami\^6, hg. von Koryo Miura. American Mathematical Society.
- Sirtautas, Justas, Anthony Pickett und A. George. 2015. Materials Characterisation and Analysis for Flow Simulation of Liquid Resin Infusion. Applied Composite Materials 22: 323–341. doi:10.1007/s10443-014-9411-6, .
- Fischer, Sebastian. 2015. Aluminium foldcores for sandwich structure application: Mechanical properties and FE-simulation. Thin-Walled Structures 90: 31–41. doi:10.1016/j.tws.2015.01.003, .
- Hoffmann, Marco, Kristian Zimmermann, Brian Bautz und Peter Middendorf. 2015. A new specimen geometry to determine the through-thickness tensile strength of composite laminates. Composites Part B: Engineering 77. doi:10.1016/j.compositesb.2015.03.020, .
2014
- Bulat, Martina und Frieder Heieck. 2014. Binder application methods for textile preforming processes. Luftfahrttechnisches Handbuch FL 21 200-02.
- Sturm, R., Yves Klett, Ch. Kindervater und H. Voggenreiter. 2014. Failure of CFRP airframe sandwich panels under crash-relevant loading conditions. Composite Structures 112: 11–21. doi:10.1016/j.compstruct.2014.02.001, .
- Gnädinger, Florian, Michael Karcher, Frank Henning und Peter Middendorf. 2014. Holistic and Consistent Design Process for Hollow Structures Based on Braided Textiles and RTM. Applied Composite Materials 21: 541–556. doi:10.1007/s10443-013-9370-3, .
- Klett, Yves und Marko Szcesny. 2014. All terrain -- all composite: Silberform expedition vehicle superstructure. JEC composites magazine: 35–36.
2013
- Böhler, Patrick, Frank Härtel und Peter Middendorf. 2013. Identification of Forming Limits for Unidirectional Carbon Textiles in Reality and Mesoscopic Simulation. Key Engineering Materials 554-557: 423–432. doi:10.4028/www.scientific.net/KEM.554-557.423, .
- Wolfinger, Benjamin. 2013. Multifunctional parts made of thermoplastic hybrid yarns. JEC Europe Magazine: 66.
- Middendorf, Peter, Frieder Heieck, Stefan Carosella und Karin Birkefeld. 2013. CFK-Handhabungsgerät macht das Leben leichter. Maschinenmarkt Composites World.
- Galappathithi, U.I.K., Anthony Pickett, Milos Draskovic, Marc Capellaro und A.K.M. de Silva. 2013. The Effect of Ply Waviness for the Fatigue Life of Composite Wind Turbine Blades. Renewable Energy & Power Quality Journal (RE&PQJ): 1195–1199.
2011
- Czichon, Steffen, Kristian Zimmermann, Peter Middendorf, Matthias Vogler und R. Rolfes. 2011. Three-dimensional stress and progressive failure analysis of ultra thick laminates and experimental validation. Composite Structures 93. doi:10.1016/j.compstruct.2010.11.009, .
- Heimbs, Sebastian, Florian Strobl und Peter Middendorf. 2011. Integration of a Composite Crash Absorber in Aircraft Fuselage Vertical Struts. International Journal of Vehicle Structures & Systems 3. doi:10.4273/ijvss.3.2.03, .
- Wolf, Daniel, Oliver Deisser, Raman Chaudhari und Holger Ahlborn. 2011. Glasfaserverbund-Werkstoffe für Fahrwerkkomponenten. ATZ - Automobiltechnische Zeitschrift 113: 832–837. doi:10.1365/s35148-011-0191-0, .
- Klett, Yves. 2011. Designing technical tessellations. In: Origami 5, hg. von Patsy Wang-Iverson, Robert J. Lang, und Mark YIM, 305–322. Hoboken: Taylor and Francis.
2010
- van den Broucke, Björn, Nahiene Hamila, Peter Middendorf, Stepan Lomov, Philippe Boisse und I. Verpoest. 2010. Determination of the mechanical properties of textile-reinforced composites taking into account textile forming parameters. International Journal of Material Forming 3. doi:10.1007/s12289-009-0680-9, .
2009
- Heimbs, Sebastian, Peter Middendorf, C. Hampf, Falk Hähnel und K. Wolf. 2009. Aircraft Sandwich Structures with Folded Core under Impact Load. Composite Solutions, Aero & Space 3.
- Erber, Andreas und Klaus Drechsler. 2009. Torsional Performance and Damage Tolerance of Braiding Configurations. JEC Magazine 52.
- Heimbs, Sebastian, S. Heller, Peter Middendorf, Falk Hähnel und J. Weiße. 2009. Low velocity impact on CFRP plates with compressive preload: Test and modelling. International Journal of Impact Engineering 36. doi:10.1016/j.ijimpeng.2009.04.006, .
- Keck, Rüdiger, Wolfgang Machunze, Wolfgang Dudenhausen und Peter Middendorf. 2009. Design, analysis, and manufacturing of a carbon-fibre-reinforced polyetheretherketone slat. Proceedings of Mechanical Engineering Vol. 223 Part G: J. Aerospace Engineering 223. doi:10.1243/09544100JAERO515, .
2008
- Drechsler, Klaus, Peter Middendorf, Van Den Broucke B. und Sebastian Heimbs. 2008. Advanced Composite Materials - Technologies, Performance and Modelling. In: Course on emerging techniques for damage prediction and failure analysis of laminated composite structures, hg. von Didier Guédra-Degeorges und Pierre Ladevèze, 147–197. Toulouse: Cépaduès-éd.
- Fuchs, U., Kristian Zimmermann, H. W. Sauer, K.-H. Trautmann und G. Biallas. 2008. Artgleiche und artverschiedene reibrührgeschweißte Verbindungen aus AA2124+25 \% SiC und AA2024. Materialwissenschaft und Werkstofftechnik 39: 531–544. doi:10.1002/mawe.200800317, .
2007
- Drechsler, Klaus, Ingo Karb, R. Kehrle und Volker Witzel. 2007. Faserverbundstrukturen - Leichtbau in Natur und Technik. Themenheft Forschung.
- Feher, L., Klaus Drechsler, J. Filsinger und R. Wiesehöfer. 2007. Microwave Processing of Advanced Composites with High Energetic Power Heating. SAMPE Journal 43: 77–82.
2006
- Llopart, Ll., B. Kurz, C. Wellhausen, M. Anglada, Klaus Drechsler und K. Wolf. 2006. Investigation of fatigue crack growth and crack turning on integral stiffened structures under mode I loading. Engineering Fracture Mechanics 73: 2139–2152. doi:10.1016/j.engfracmech.2006.04.005, .
- Feher, L., M. Thumm und Klaus Drechsler. 2006. Gigahertz and Nanotubes -- Perspectives for Innovations with Novel Industrial Microwave Processing Technology. Advanced Engineering Materials 8: 26–32. doi:10.1002/adem.200500148, .
2005
- Veldman, S. L., O. K. Bergsma, A. Beukers und Klaus Drechsler. 2005. Bending and optimisation of an inflated braided beam. Thin-Walled Structures 43: 1338–1354. doi:10.1016/j.tws.2005.06.004, .
Tagungs- und Konferenzbeiträge
2025
- Grisin, Benjamin, Stefan Carosella und Peter Middendorf. 2025. Vakuumkammer Infusion zur Herstellung von TowPregs und faserverstärkten Verbundkunststoffen. In: 29. Stuttgarter Kunststoffkolloquium, hg. von Christian Bonten und Marc Kreutzbruck. Schriftenreihe / Institut für Kunststofftechnik. Stuttgart: IKT, Universität Stuttgart, Februar.
- Platzer, Dominik, Stefan Carosella und Peter Middendorf. 2025. Nachträgliche Kohlenstoffkurzfaserverstärkung stereolithografisch gefertigter Strukturen. In: 29. Stuttgarter Kunststoffkolloquium, hg. von Christian Bonten und Marc Kreutzbruck. Schriftenreihe / Institut für Kunststofftechnik. Stuttgart: IKT, Universität Stuttgart, Februar.
2024
- Bauer, Johannes, Johannes Baur, Stefan Carosella und Peter Middendorf. 2024. Laser-Induced Periodic Surface Structures as a Novel fiber Surface Treatment in Composite Manufacturing. In: Aachen Reinforced! Symposium. Dezember.
- Baur, Johannes, O. Benetreau, Stefan Carosella und Peter Middendorf. 2024. Design and Manufacturing of Ultra-Lightweight Cabin Interior Panels for Urban Air Mobility Using Tailored Fiber Placement. In: Aachen Reinforced! Symposium. Dezember.
- Take, Jens und Peter Middendorf. 2024. Energieeffiziente UV-Aushärtung von glasfaserverstärkten Kunststoffen im RTM-Prozess. In: . 30. Leichtbauforum des LBZ. Nürtingen, DE, November.
- Take, Jens. 2024. Studies of UV LED-cured GFK composites in seconds. In: . 13th Kompozyt-Expo. Krakow, Poland, Oktober.
- Frank, Niklas, Johannes Baur, Christian Strohl, Albert Albers, Tobias Duser, Peter Middendorf und Thomas Graf. 2024. Design, Manufacturing and Recycling of Selectively Reinforced Hybrid NFRP Components. In: DS 133: Proceedings of the 35th Symposium Design for X (DFX2024), 135–142. The Design Society, September. doi:10.35199/dfx2024.14, .
- Strohl, C., J. Powell, J. Baur, J. Michel, C. Hagenlocher, D. Holder und T. Graf. 2024. Separation of flax and carbon fiber hybrid composites by laser-based pyrolysis. Procedia CIRP 124 (September): 42–45. doi:10.1016/j.procir.2024.08.067, .
- Take, Jens und Peter Middendorf. 2024. Studies of UV LED-cured GFK Composites with the RTM Process. In: . TexComp-15 Conference. Leuven, Belgium, September.
- Baur, Johannes, M. Horvat, Stefan Carosella und Peter Middendorf. 2024. Studies on the Ultrasonic Welding of Thermoplastic NFRPs. In: . TexComp-15 Conference. Leuven, Belgium, September.
- Bauer, Johannes, Klaus Heudorfer, Yavuz Caydamli, Michael R. Buchmeiser und Peter Middendorf. 2024. Manufacturing of Transparent Glass Fiber Reinforced Composites Using Light Resin Transfer Molding Techniques with a Flexible Polycarbonate Tooling Concept. In: CAMX 2024. NA SAMPE, September. doi:10.33599/nasampe/c.24.0250, .
2023
- Baur, Johannes. 2023. Optimization of Sustainable Natural Fiber Reinforced Composites. In: . 3rd Plasma Nanotechnologies and Bioapplications Workshop. Hustopece, Czech Republic, Oktober.
- Take, Jens. 2023. Recyclable natural fiber-polymer gypsum composites and an automated processing method for the production of hybrid lighting structures. In: . 3rd Plasma Nanotechnologies and Bioapplications Workshop. Hustopece, Czech Republic, Oktober.
- Helber, Florian, Stefan Carosella und Peter Middendorf. 2023. Automated preforming with a smart mould approach for efficient liquid resin infusion in aerospace applications. In: Proceedings of the Twenty-third international conference on composite materials (ICCM 23). Juli.
- Bauer, Johannes, Klaus Heudorfer, Yavuz Caydamli, Bruno Gompf, Michael R. Buchmeiser und Peter Middendorf. 2023. A Method to Manufacture Transparent Composites by Optimizing Refractive Index Match of Fiber and Polymer. In: 28. Stuttgarter Kunststoffkolloquium, hg. von Christian Bonten und Marc Kreutzbruck. Schriftenreihe / Institut für Kunststofftechnik. Stuttgart: IKT Universität Stuttgart, Februar.
- Baur, Johannes, Christian Strohl, Florian Helber, Thomas Graf und Peter Middendorf. 2023. Untersuchungen zu Herstellung, Einsatz und Recycling von nachhaltigen FVK. In: 28. Stuttgarter Kunststoffkolloquium, hg. von Christian Bonten und Marc Kreutzbruck. Schriftenreihe / Institut für Kunststofftechnik. Stuttgart: IKT Universität Stuttgart, Februar.
2022
- Ackermann, Annika C., Michael Fischer, Alexander Wick, Stefan Carosella, Bronwyn L. Fox und Peter Middendorf. 2022. Investigation of the Thermal and Mechanical Properties of Composite Materials with Amine-Functionalized Reduced Graphene Oxide Inclusions. In: Proceedings of the 20th European Conference on Composite Materials - Composites Meet Sustainability (Vol 1-6). Dezember.
- Liebl, Michael, Mathias Engelfried, Stefan Carosella und Peter Middendorf. 2022. Determination of the Bending Stiffness of Spread Carbon Fibre Tows Applied with Reactive Binder. In: Proceedings of the Munich Symposium on Lightweight Design 2021, hg. von Jasper Rieser, Felix Endress, Alexander Horoschenkoff, Philipp Höfer, Tobias Dickhut, und Markus Zimmermann, 59–67. Berlin, Heidelberg: Springer Berlin Heidelberg, August. doi:10.1007/978-3-662-65216-96, .
- Mesarosch, Felix, Tristan Schlotthauer, Marlies Springmann, Johannes Schneider und Peter Middendorf. 2022. Topology Optimization and Production of a UAV Engine Mount Using Various Additive Manufacturing Processes. In: Proceedings of the Munich Symposium on Lightweight Design 2021, hg. von Jasper Rieser, Felix Endress, Alexander Horoschenkoff, Philipp Höfer, Tobias Dickhut, und Markus Zimmermann, 124–135. Berlin, Heidelberg: Springer Berlin Heidelberg, August. doi:10.1007/978-3-662-65216-912, .
- Helber, Florian, Stefan Carosella und Peter Middendorf. 2022. Quantitative Assessment of Reactive and Non-Reactive Binder Systems on First Ply Adhesion for Dry Fiber Placement Processes. In: . 25th International ESAFORM Conference on Material Forming. April.
2021
- Springmann, M., S. Mirzaei und P. Middendorf. 2021. Printing Path Based Modeling of FFF Meso-structures for Finite Element Analysis. In: . NAFEMS World Congress. Oktober.
- Raichle, Andreas, Andreas Damm und Peter Middendorf. 2021. Data Requirements for Detecting Collision Positions on Fiber Composite Plates Using Artificial Intelligence. In: . NAFEMS World Congress. Oktober.
- Schlotthauer, T., A. Geitner, C. Seifarth, O. Schendel, T. Lück, R. Kaindl, D. Kopp, u. a. 2021. Reinforcement of stereolithographic manufactured structures by the subsequent infusion of short carbon fibers. In: . SAMPE Europe Conference. Baden/Zürich -- Schweiz, September.
- Liebl, Michael, Mathias Engelfried, Stefan Carosella und Peter Middendorf. 2021. Investigation of the friction behaviour of spread carbon fibre tows with reactive binder. In: . SAMPE Europe Conference. Baden/Zürich -- Schweiz, September.
- Kaindl, R., D. Kopp, S. Spalt, T. Schlotthauer, C. Seifarth, O. Schendel, T. Lück, u. a. 2021. Friction- and wear-reducing atmospheric pressure plasma molybdenum disulfide -- graphite coatings on fibre-reinforced composites manufactured by stereolithography. In: . EUROMAT. September.
- Heieck, Frieder, Fabian Muhs, Marlies Springmann, Nicolas Unger und Philipp Weißgraeber. 2021. Advancing from Additive Manufacturing to Large-Scale Production of Face Shields During the COVID-19 Pandemic. Advances in Automotive Production Technology -- Theory and Application 110 (Juni): 394–404. doi:10.1007/978-3-662-62962-846, .
- Grisin, Benjamin, Stefan Carosella und Peter Middendorf. 2021. Dry Fibre Placement - Einfluss von Prozessparametern auf mechanische Laminateigenschaften und Infusionsverhalten. In: . 27. Stuttgarter Kunststoffkolloquium. März.
- Springmann, M., T. Schlotthauer, A. Peter, H. Altmann, J. Musso und P. Middendorf. 2021. Identifikation geeigneter Photopolymerezur Verarbeitung in Zwei-Photonen-SLA-Verfahren. In: . 27. Stuttgarter Kunststoffkolloquium. März.
- Baranowski, Michael, Tristan Schlotthauer, Markus Netzer, Philipp Gönnheimer, Sven Coutandin, Jürgen Fleischer und Peter Middendorf. 2021. Hybridization of Fused Filament Fabrication Components by Stereolithographic Manufactured Thermoset Inserts. In: . ICMEP 2021 - The 10th International Conference on Manufacturing Engineering and Processes. Singapore, März. doi:10.1007/978-981-16-3934-01, .
- T. Schlotthauer, S. R. Raisch, A. Dorneich, T. Heckner, T. Mohr und P. Middendorf. 2021. Teilindividualisierte und nachverfolgbare Spritzgussbauteile durch In-situ-Anbindung additiv hergestellter Subkomponenten. In: . 27. Stuttgarter Kunststoffkolloquium. Stuttgart, März.
2020
- Fial, J., Stefan Carosella und Peter Middendorf. 2020. Enhancing textile forming using textile-applied strain sensors and segmented blank holder systems. In: . SCAP 2020 - Stuttgart Conference on the Automotive Production. Stuttgart, Oktober.
- Dittmann, Jörg, M. Vinot, Peter Middendorf und Nathalie Toso. 2020. Simulation supported manufacturing of profiled composite parts with the braiding technique. In: . SCAP 2020 - Stuttgart Conference on the Automotive Production. Stuttgart, Oktober.
- Helber, Florian, Stefan Carosella und Peter Middendorf. 2020. Multi-robotic composite production of complex and large-scaled components for the automotive industry. In: . SCAP 2020 - Stuttgart Conference on the Automotive Production. Stuttgart, Oktober.
- Facciotto, Silvio, Daniel Sommer, A. Haufe, M. Helbig und Peter Middendorf. 2020. Modelling Defects of Unhardened Adhesives Resulting from Handling and Warpage: Viscous Fingering. In: . SCAP 2020 - Stuttgart Conference on the Automotive Production. Stuttgart, Oktober.
- Schlotthauer, Tristan. 2020. Stereolithografie-Materialien, Prozesse und Plasma-Nachbehandlungsverfahren für dauerbeständige Automobilanwendungen. In: . Technologiegespräch Materialinnovationen für die additive Fertigung. Oktober.
- Nitsche, Jan, Tristan Schlotthauer, F. Hermann und Peter Middendorf. 2020. Experimental and theoretical study on depth of cure during UV post-curing of photopolymers used for additive manufacturing. In: . SCAP 2020 - Stuttgart Conference on the Automotive Production. Stuttgart, Oktober. doi:10.1007/978-3-662-62962-840, .
- Fial, J., S. Carosella und P. Middendorf. 2020. Forming Characterization of Non-Crimp Fabrics using Textile-applied printed Strain Sensors. In: . SAMPE 2020. Amsterdam, September.
- Albrecht, Fabian, Christian Poppe, J. Fial, Frank Henning und P. Middendorf. 2020. Effect of process routing (direct vs. preformed) on part infiltration during Wet Compression Molding (WCM) of a complex demonstrator. In: . SAMPE 2020. Amsterdam, September.
- Fial, J., S. Carosella, L. Ring und P. Middendorf. 2020. Shear Characterization of Reinforcement Fabrics using printed Strain Sensors. In: . ESAFORM2020. Cottbus, Mai.
2019
- Ackermann, Annika C., S. Carosella, P. Middendorf und Bronwyn Fox. 2019. Einfluss der Oberflächenfunktionalisierung von Graphenpartikeln auf die Eigenschaften und die Verarbeitung von Nanokompositen. In: . Hybride Materialien - Nano goes Macro. Nuremberg, November.
- Springmann, Marlies. 2019. Verbindung lastpfad-optimierter FVK Strukturen mit additiv gefertigten Elementen. In: . AFBW AG Simulation. Denkendorf, Oktober.
- Klett, Yves, P. Middendorf, Fabian Muhs, Werner Sobek, Weidner und Walter Haase. 2019. Exploration of Compliant Hinges in Origami-based Structures. In: . IASS Symposium 2019. Barcelona, Spain, Oktober.
- Helber, Florian, Marko Szcesny, S. Carosella und P. Middendorf. 2019. Tack and Binder Solubility Investigations on Reactive and Non-Reactive Binder Systems. In: . SAMPE Europe Conference 2019. Nantes, France, September.
- Dittmann, Jörg, Andreas Friedrichs, Silvio Facciotto und Peter Middendorf. 2019. Dual Phase Void Prediction in Microscopic Yarn Models. In: . ICCM22 - 22nd International Conference on Composite Materials. Melbourne, Australia, August.
- Klett, Yves. 2019. Von Stricklieseln und Papierfliegern. In: . WiWeb Kolloquium 2019. Erding, August.
- Klett, Yves. 2019. When four creases meet: Technical tessellation tales. In: . IDETC-CIE 2019 International Design Engineering Technical Conferences & Computers and Information in Engineering Conference. Anaheim, USA, August.
- Reghat, Mojdeh, Adin Min Tang, Yehuda Wiezman, Franz Konstantin Fuss, Peter Middendorf, Robert Bjekovic, Lachlan Hyde, Bronwyn Fox, Azadeh Mirabedini und Nishar Hameed. 2019. Smart Graphene-Enabled Composite. In: . ICCM22 - 22nd International Conference on Composite Materials. Melbourne, Australia, August.
- Helber, Florian, Marko Szcesny, S. Carosella und P. Middendorf. 2019. Enhancements on Automated Preforming for Composite Structures. In: . ICCM22 - 22nd International Conference on Composite Materials. Melbourne, Australia, August.
- Oei, Marius, Yves Klett, Nadine Harder, Daniela Flemming und Oliver Sawodny. 2019. Modelling the Flow and Heat Transfer Characteristics of Perforated Foldcore Sandwich Composites for Application in Room Air Conditioning. In: . 2019 IEEE 15th International Conference on Automation Science and Engineering (CASE). Vancouver, Canada, August. doi:10.1109/COASE.2019.8842913, .
- Klett, Yves. 2019. Paper, planes and more -- Exploring the potential of origami, from aerospace to architecture. In: . Seminar at Georgia Tech. Atlanta, USA, August.
- Ackermann, Annika C., Stefan Carosella, Peter Middendorf und Bronwyn Fox. 2019. Effect of Surface Functionalization of Graphene Particles on the Properties of Nanocomposites. In: . ICCM22 - 22nd International Conference on Composite Materials. Melbourne, Australia, August.
- Middendorf, Peter. 2019. Composites 4.0: From Design to Automated Manufacturing. In: . ICCM22 - 22nd International Conference on Composite Materials. Melbourne, Australia, August.
- Damm, A., Karim Bahroun und P. Middendorf. 2019. A Low-Cost Flow Front Monitoring System. In: . ICCM22 - 22nd International Conference on Composite Materials. Melbourne, Australia, August.
- Lux, Benedikt, J. Fial, Olivia Schmidt, S. Carosella, P. Middendorf und Bronwyn Fox. 2019. Comparison of picture frame devices and analysis of locking angle for fabrics with different cross-ply angles. In: . ICCM22 - 22nd International Conference on Composite Materials. Melbourne, Australia, August.
- Klett, Yves und Peter Middendorf. 2019. Exploration of Plastically Annealed Lamina Emergent Origami Structures. In: . EMI Engineering Mechanics Institute Conference 2019. Pasadena, USA, Juni.
- Heudorfer, Klaus. 2019. Introduction of the Institute of Aircraft Design and EFFICOMP activities. Presentation of the Advanced Ply Placement (APP) results developed during the EU-Project Efficient Composite Parts Manufacturing (EFFICOMP). In: . National Composite Center (NCC). Nagoya University, Japan, Mai.
- Heudorfer, Klaus. 2019. Herstellung von GFK-Spoilern mit Niederdruck-Harzinjektion und Fotopolymerisation. In: . LBZ-Workshop \textquotedblLeichtbau wird leichter mit UV-Anwendungen\textquotedbl. IST-Metz, Mai.
- F. Helber, S. Carosella und P. Middendorf. 2019. Advanced Ply Placement -- Neue Ansätze für die automatisierte Fertigung von Faserverbundstrukturen. In: . 26. Stuttgarter Kunststoffkolloquium. Stuttgart, Germany, März.
- M. Blandl und P. Middendorf. 2019. TowPregs -- auf ihrem Weg zur Serie. In: . 26. Stuttgarter Kunststoffkolloquium. Stuttgart, Germany, März.
- T. Schlotthauer und P. Middendorf. 2019. Prozessgrenzen bei der stereolithografischen Herstellung von Kohlenstoff-kurzfaserverstärktem Kunststoff. In: . 26. Stuttgarter Kunststoffkolloquium. Stuttgart, Germany, März.
- J. Dittmann und P. Middendorf. 2019. Permeabilitätsmessungen bei technischen Textilien und die Durchführung von Benchmarkstudien. In: . 26. Stuttgarter Kunststoffkolloquium. Stuttgart, Germany, März.
- Kretschmer, Matthias, Jason Jonkman und Po Wen Cheng. 2019. Validation of FAST.Farm considering structural loads at alpha ventus. In: . Wind Energy Science Conference 2019. Cork. doi:10.5281/zenodo.3550524, .
2018
- Facciotto, Silvio, A. Pouchias, Tifkitsis K. I., Anthony Pickett, J. Stein, A. A. Skordos und C. Miguel-Giraldo. 2018. Variability propagation, process monitoring and simulation tools for predictive modelling of RTM processes. In: . 8th EASN-CEAS International Workshop. Glasgow, Scotland, September.
- Helber, Florian, Andreas Amann, Stefan Carosella und Peter Middendorf. 2018. Intrinsic Fibre Heating: A novel Approach for Automated Dry Fibre Placement. In: . TEXCOMP-13. Milano, Italy, September.
- Heudorfer, Klaus, Mathias Engelfried, J. Fial, S. Carosella und P. Middendorf. 2018. Characterisation of the Forming properties of wide unidirectional prepreg tapes using the advanced ply placement (APP) process. In: . 8th EASN - CEAS International Conference on Manufacturing for Growth & Innovation. Glasgow, Scotland, September.
- Fial, J., M. Harr, Patrick Böhler und Peter Middendorf. 2018. Automated wet compression moulding of load-path optimized TFP preforms with low cycle times. In: . 13th international conference on textile composites (Texcomp). Milan, Italy, September.
- Klett, Yves. 2018. PALEO: Plastically Annealed Lamina Emergent Origami. In: . ASME 2018 International Design Engineering Technical Conferences and Computers and Information in Engineering Conference. Quebec, Canada, August.
- Helber, Florian, Marko Szcesny, Stefan Carosella und Peter Middendorf. 2018. Advanced Ply Placement: A novel Approach for the Automated Placement of dry Fibres from Bio-Based Materials. In: . ICMAC 2018. Nottingham, UK, Juli.
- Facciotto, Silvio, Anthony Pickett, Lingua A., Jorge Ignacio López Palomarez und Peter Middendorf. 2018. Effect of Fabric Deformation and Flow Velocity on Generation of Porosity in Infusion Processes. In: . FPCM - 14th International Conference on Flow Processes in Composite Materials. Lule\aa,~Sweden, Juni.
- Dittmann, J., Patrick Böhler, M. Vinot, C. Liebold, F. Fritz, A. Pau, N. Dölle, u. a. 2018. Der Digitale Prototyp. In: . Technologietag Hybrider Leichtbau. Stuttgart, Juni.
- Schwingel, Johannes, J. Wellekötter, S. Baz, P. Middendorf, C. Bonten und Götz Gresser. 2018. Resource and Energy Efficient Manufacturing of Automotive Lightweight Parts Made of Recycled Material. In: . ECCM 18 - 18th European Conference on Composite Materials. Athens, Greece, Juni.
- Dittmann, Jörg und Peter Middendorf. 2018. Experimental Validation of Numerical Dual-Scale Permeability Prediction. In: . FPCM - 14th International Conference on Flow Processes in Composite Materials. Lule\aa,~Sweden, Juni.
- Fial, J., J. Hüttl, P. Middendorf und Frank Henning. 2018. Ganzheitliche Untersuchung der Nasspresstechnologie anhand ausgewählter Prozess- und Simulationsrouten. In: . 5. Technologietag hybrider Leichtbau. Stuttgart, Juni.
- Fial, J., Patrick Böhler und Peter Middendorf. 2018. Automated wet compression moulding of load-path optimised TFP preforms with low cycle times. In: . 29th SICOMP Conference on Manufacturing and Design of Composites. Lule\aa,~Sweden, Mai.
- Klett, Yves und Peter Middendorf. 2018. BiSKiTs: Bistable Kirigami Tessellations. In: . EMI Engineering Mechanics Institute Conference 2018. Boston, USA, Mai.
- Sommer, Daniel, B. Bender, F. Eidmann und Peter Middendorf. 2018. Manufacturing of hybrid steel-FRP specimens for the characterization of material properties. In: . 29th SICOMP Conference on Manufacturing and Design of Composites. Lule\aa,~Sweden, Mai.
- Fial, J., Stefan Carosella, M. Langheinz, P. Wiest und Peter Middendorf. 2018. Novel Textile Characterisation Approach Using An Embedded Sensor System And Segmented Textile Manipulation. In: . ESAFORM 2018. Palermo, Italy, April.
- Selvarayan, Sathis, Simon Küppers, Benjamin Lehman, Lena Müller, Dennis Zink, Daniel Michaelis, Stefan Zuleger, Karim Bahroun, Peter Middendorf und Götz Gresser. 2018. Integrated FRP battery thermal management module. In: . 8. WerkstoffPlus Auto. Stuttgart, Februar.
- Klett, Yves. 2018. Kleine Falten, große Wirkung: Kostengünstige und leistungsfähige Leichtbaulösungen. In: . 2. Kongress Innovation+: Papier, Textil & Folie. Regensburg, Februar.
- Klett, Yves. 2018. Kostengünstige und leistungsfähige Lösungen für multifunktionalen Leichtbau. In: . innovation+: papier, textil & folie. Regensburg, Januar.
2017
- Draskovic, Milos, A. K. Pickett, Stefan Carosella, Luise Kärger, Frank Henning und Peter Middendorf. 2017. Accelerated Residual Strength After Fatigue Testing Using In-Situ Image Processing for Damage Detection. In: . SAMPE Conference 2017. Stuttgart, November.
- Klett, Yves. 2017. Overview of Mechanical Properties of Foldcore-based Sandwich Structures. In: . The Second International Workshop on Origami Engineering, Tianjin, China. Tianjin, China, November.
- Gizik, Daniel, Christian Metzner, Christian Weimer und Peter Middendorf. 2017. Heavy tow carbon fibers for aerospace applications. In: . Aachen-Dresden-Denkendorf International Textile Conference 2017. Stuttgart, November.
- Helber, Florian, Bettina Schrick, Stefan Carosella und Peter Middendorf. 2017. Tailored Preform Production with Customizable UD Materials for Hybrid Material Design. In: . SAMPE Conference 2017. Stuttgart, November.
- Michaelis, D. und Peter Middendorf. 2017. Tensile Testing of Biaxially Braided Carbon Composites. In: . SAMPE Conference 2017. Stuttgart, November.
- Fernández, D., B. Begemann, Peter Middendorf und P. Horst. 2017. Untersuchung des Beul- und Tragverhaltens von Selektiv Genähten, Versteiften FKV-Paneelen unter Mehraxialer Belastung. In: . 66. Deutscher Luft- und Raumfahrtkongress. München, September.
- Heudorfer, Klaus, Mathias Engelfried, J. Fial, Stefan Carosella und Peter Middendorf. 2017. Investigation of a New out of Autoclave Placement Process, Mould Concepts/Release Strategies and Reusable Heated Bagging Material. In: . 7th EASN International Conference. Warsaw, Poland, September.
- Klett, Yves. 2017. Kleine Knicke, große Wirkung -- faltungsbasierte Sandwichkerne. In: . 2. Bremer Faserverbundtage. Bremen, September.
- Dittmann, Jörg, S. Hügle, P. Seif, Kaufmann L. und Peter Middendorf. 2017. Permeability Prediction Using Porous Yarns in a Dual-Scale Simulation with Openfoam. In: . ICCM21 - 21st International Conference on Composite Materials. Xi’an, China, August.
- Klett, Yves. 2017. Experimental Characterization of Pressure Loss Caused by Flow Through Foldcore Sandwich Structures. In: . ASME 2017 International Design Engineering Technical Conferences and Computers and Information in Engineering Conference. Cleveland, OH, USA, August.
- Sommer, Daniel und Iskender Silak. 2017. Untersuchung von hybriden Klebeverbindungen während des Aushärteprozesses in einem gläsernen Ofen. In: . CCeV Engineering/Klebtechnik/NDE. Augsburg, Juli.
- Schwingel, Johannes, S. Baz, J. Wellekötter und Stefan Carosella. 2017. Resource and Energy Efficient Manufacturing of Automotive Lightweight Parts Made of Recycled Material. In: . BW Forschungstag 2017. Stuttgart, Juni.
- Klett, Yves, P. Middendorf, Michael Heidingsfeld, Werner Sobek und Walter Haase. 2017. Potential of Origami-Based Shell Elements as Next-Generation Envelope Components. In: . IEEE International Conference on Advanced Intelligent Mechatronics (AIM 2017). Munich, Juni.
- Poppe, Christian, J. Fial, Luise Kräger, Stefan Carosella, Clemens Zimmerling, Fabian Albrecht, Milos Draskovic, Mathias Engelfried, Peter Middendorf und Frank Henning. 2017. Zeit- und kosteneffiziente Prozess- und Produktentwicklung für den Hochleistungs-Faserverbundleichtbau mittels Nasspresstechnologie. In: . 4. Technologietag Hybrider Leichtbau. Stuttgart, Mai.
- Schrick, Bettina und Stefan Carosella. 2017. Anlagentechnik für Maßgeschneiderte Preform Konstruktion und Produktion. In: . 4. Technologietag Hybrider Leichtbau. Stuttgart, Mai.
- Liebold, C., A. Haufe, M. Vinot, J. Dittmann, Patrick Böhler, H. Finckh und P. Middendorf. 2017. The Digital Prototype as Part of Envyo - Developent History and Applications within the ARENA2036 Environment. In: . 11th European LS-DYNA Conference. Salzburg, Austria, Mai.
- Facciotto, Silvio, Jörg Dittmann, A. K. Pickett und Peter Middendorf. 2017. Characterization and Modelling of Local Compaction Effect on Permeability in Infusion Processes. In: . 8th International Conference on Composites Testing and Model Identification. Leuven, Belgium, April.
- Draskovic, Milos, A. K. Pickett und Peter Middendorf. 2017. Influence of Ply Waviness on the Residual Strength After Fatigue in GFRP - Comparison of Localized and Uniform Defects. In: . 8th International Conference on Composites Testing and Model Identification. Leuven, Belgium, April.
- Gnädinger, Florian, Peter Middendorf und Bronwyn Fox. 2017. Influence of Carbon Fibre Sizings and Matrix Resins on Fibre-Matrix Adhesion: Flexure and Shear Measurements of CFRP-Laminates. In: . 25. Stuttgarter Kunststoffkolloquium. Stuttgart, März.
- Wellekötter, J., C. Bonten, S. Baz, T. Gresser, Johannes Schwingel und Peter Middendorf. 2017. Resource-Efficient Lightweight Design Due to New Recycling Concept. In: . 25. Stuttgarter Kunststoffkolloquium. Stuttgart, März.
- Szcesny, Marko, Klaus Heudorfer, Peter Middendorf, R. Blumrich, Riegel M. und J. Wiedemann. 2017. Design, Manufacturing and Application of Carbon Fiber Reinforced Airfoils Used to Create Turbulence and Gusts in a Vehicle Wind Tunnel. In: . 25. Stuttgarter Kunststoffkolloquium. Stuttgart, März.
- Wolfinger, Benjamin, Stefan Carosella und Peter Middendorf. 2017. Complex Carbon/PA6 Hybrid Yarn Structures Made by Tailored Fibre Placement. In: . 25. Stuttgarter Kunststoffkolloquium. Stuttgart, März.
- Heudorfer, Klaus, Stefan Carosella und Peter Middendorf. 2017. Compression Wet Moulding as Alternative to RTM. In: . 25. Stuttgarter Kunststoffkolloquium. Stuttgart, März.
- Bauer, Felix, Peter Middendorf, Manuel Kempf und Frank Weiland. 2017. Basalt Fiber Reinforced Composites for Elevated Application Temperatures. In: . 25. Stuttgarter Kunststoffkolloquium. Stuttgart, März.
2016
- Michaelis, Daniel. 2016. Prüfverfahren von CFK-Geflechten. In: . CCeV Thementag Flechten. Stuttgart, Dezember.
- Schwingel, Johannes. 2016. Resource and Energy Efficient Manufacturing of Automotive Lightweight Parts Made of Recycled Material. In: . International Textile Conference 2016 (Aachen-Dresden-Denkendorf). Dresden, November.
- Dittmann, Jörg, Patrick Böhler, D. Michaelis und Peter Middendorf. 2016. DigitPro -- Aufbau eines digitalen Prototyps für den industriellen Großeinsatz 4.0. In: . NAFEMS Seminar - Simulation von Composites -- Bereit für Industrie 4.0. Hamburg, Oktober.
- Dittmann, Jörg und Peter Middendorf. 2016. ARENA2036 -- Above-and-Beyond. In: . LS-Dyna User Forum. Bamberg, Oktober.
- Middendorf, Peter. 2016. DigitPro: Ganzheitlicher digitaler Prototyp für industriellen FVK-Leichtbau. In: . Forel Kolloquium. Oktober.
- Dittmann, Jörg und Peter Middendorf. 2016. DigitPro - Ganzheitlicher digitaler Prototyp im Leichtbau für die Großserienproduktion. In: . Fachtagung Wissenschaft und Wirtschaft nachhaltig vernetzen. Berlin, Juni.
- Tartler, Manuel, D. Hägele, J. Fial, Mathias Engelfried, Ingo Karb und Peter Middendorf. 2016. Investigation and Simulation of Forming Behaviour of Preforms Made by Direct Fibre Placement. In: . ECCM17 17th European Conference on Composite Materials. Munich, Juni.
- Fial, J., Patrick Böhler und Peter Middendorf. 2016. Advanced Forming of Tailored Textiles Using Locally Modified Properties for Optimized Lightweight Structures. In: . ECCM17 17th European Conference on Composite Materials. Munich, Juni.
- Heieck, Frieder und Peter Middendorf. 2016. Effect of the Cover Factor of 2D Biaxial and Triaxial Braided Carbon Composites on Their In-Plane Mechanical Properties. In: . ECCM17 17th European Conference on Composite Materials. Munich, Juni.
- Dittmann, Jörg, D. Michaelis, Patrick Böhler und Peter Middendorf. 2016. DigitPro - Validating The Link Between Braiding Simulation, Infiltration and Mechanical Testing. In: . ECCM17 17th European Conference on Composite Materials. Munich, Juni.
- Michaelis, D. und Peter Middendorf. 2016. Characteristic Load Cases of Biaxial Braids. In: . ECCM17 17th European Conference on Composite Materials. Munich, Juni.
- Gizik, Daniel, Christian Metzner und Peter Middendorf. 2016. Spreading of Heavy Tow Carbon Fibers for the use in aircraft structures. In: . ECCM17 17th European Conference on Composite Materials. Munich, Juni.
- Engelfried, Mathias, Tomas Nosek, Frieder Heieck, Patrick Böhler und Peter Middendorf. 2016. Lowflip - Draping Simulation of Prepregs at Mesoscopic and Macroscopic Level. In: . d. Munich, Juni.
- Zink, Dennis, C. Awe und Peter Middendorf. 2016. Automated Design Approach and Potential Assessment of Composite Structures: Fast Analytical Engineering Tool for Multiple Load Cases. In: . ECCM17 17th European Conference on Composite Materials. Munich, Juni.
- Vinot, M., M. Holzapfel, D. Michaelis, Jörg Dittmann, Patrick Böhler, Peter Middendorf und C. Liebold. 2016. Numerische Prozesskette für die Auslegung von geflochtenen Fahrzeugkomponenten - Nutzen und Herausforderungen. In: . Symposium Faszination Hybrider Leichtbau. Wolfsburg, Mai.
- Meiler, S., P. Fey, Marc Kreutzbruck, Milos Draskovic und Peter Middendorf. 2016. Nondestructive Testing of CFRP with Thermoplastic Matrix. In: . ANTEC. Indianapolis, USA, Mai.
- Klein, Linda und Peter Middendorf. 2016. Designte Sensorfunktionalität im Automobilleichtbau mit Faserverbundkunststoff (eine Systembetrachtung). In: . 4SMARTS Symposiums. Darmstadt, April. doi:10.1515/9783110469240-018, .
- Blandl, M. 2016. Development of an Alternative Method for Fiber Impregnation. In: . EPTA - 13th World Pultrusion Conference. Prague, Czech Republic, März.
- Carosella, Stefan. 2016. Recent Developments and Research Results regrading TFP-Technology at the Institute of Aircraft Design. In: . CCeV Thementag Tailored Fiber Placement. Dresden, März.
2015
- Adebahr, W., Ronny Sachse, Peter Middendorf und Marc Kreutzbruck. 2015. Crack growth monitoring at CFRP adhesive bondings. In: . Polymer Processing Society Conference 2015. Graz, Austria, Oktober. doi:10.1063/1.4965563, .
- Fuhr, Jan-Philipp und Peter Middendorf. 2015. Validierung der virtuellen Auslegungsprozesskette für schichtbasierte Faserverbundstrukturen. In: . ESI DACH Forum. Bamberg, Oktober.
- Böhler, Patrick und Peter Middendorf. 2015. Mesoskopisches Drapieren - Simulation und Vailidierung. In: . LBZ-Tagung. Pfinztal, Oktober.
- Klein, Linda und Peter Middendorf. 2015. Functionalized lightweight parts: Application of LCM for the integration of automotive sensors in CFRP structures. In: . Polymer Processing Society Conference 2015. Graz, Austria, September. doi:10.1063/1.4965560, .
- Bezerra, R., F. Wilhelm, S. Strauß und Holger Ahlborn. 2015. Manufacturing of Complex Shape Composite Parts through the Combination of Pull-Braiding and Blow Moulding. In: . ICCM20 - 20th International Conference on Composite Materials. Copenhagen, Denmark, Juli.
- Heieck, Frieder und Peter Middendorf. 2015. Technological approaches on cost reduction challenges for thermoset composites. In: . JEC Americas Conference. Houston, USA, Juli.
- Fernández, D. und Peter Middendorf. 2015. Study of the Influence of UV-Light on CFRP Laminates Stitched with Aramid Thread. In: . ICCE-23. Chengdu, China, Juli.
- Heieck, Frieder. 2015. Quality Assessment of 2D Braided Composites with Optical Measurement Techniques. In: . 18th International Conference on Composite Structures. Lisbon, Portugal, Juni.
- Böhler, Patrick, Stefan Carosella, C. Götz und Peter Middendorf. 2015. Reverse Draping - oder - Woher kommen Fasergerechte Ablagepfade für den TFP-Prozess. In: . Compoform 2015. Munich, Mai.
- Blandl, M. 2015. Alternative TowPregs - A further developed impregnation technology for semi-finished fiber products. In: . Hannovermesse 2015. Hannover, April.
- Fey, P., G. Busse, Marc Kreutzbruck, D. Michaelis und Peter Middendorf. 2015. Non-Destructive Monitoring of Damage in CFRP Laminates using Ultrasonic Birefringence. In: . ANTEC 2015. Orlando, USA, März.
- Reiling, J. M., Peter Middendorf und M. Sindel. 2015. Quality assurance of adhesive processes in the body shop. In: . 15thStuttgart International Symposium on Automotive and Engine Technology. Stuttgart, März.
- Gnädinger, Florian. 2015. Einfluss der Faserschlichte auf die Faser-Matrix Haftung. Qualitative Untersuchungen für verschiedene Polymerschlichten und -harzsysteme. In: . 24. Stuttgarter Kunststoffkolloquium. Stuttgart, Februar.
- Dittmann, Jörg, A. Neu und Peter Middendorf. 2015. Permeabilitätsbestimmung für die optimierte Herstellung von endlosfaserverstärkten Kunststoffen. In: . 24. Stuttgarter Kunststoffkolloquium. Stuttgart, Februar.
- Dittmann, Jörg. 2015. Permeabilitätsbestimmung für die optimierte Herstellung von Faser-Kunststoff-Verbunden. In: . 24. Stuttgarter Kunststoffkolloquium. Stuttgart, Februar.
- Ahlborn, Holger. 2015. Herstellung komplexer FVK-Bauteile mittels Flechtpultrusion und Blasumformung. In: . 24. Stuttgarter Kunststoffkolloquium. Stuttgart, Februar.
- Reiling, J. M. 2015. Eigenschaftsprofil von Klebverbindungen im Karosseriebau. In: . 24. Stuttgarter Kunststoffkolloquium. Stuttgart, Februar.
- Blandl, M. 2015. Entwicklung eines alternativen Imprägnierverfahrens für Faserhalbzeuge. In: . 24. Stuttgarter Kunststoffkolloquium. Stuttgart, Februar.
- Fey, P., D. Michaelis, Peter Middendorf, G. Busse und Marc Kreutzbruck. 2015. Charakterisierung anisotroper Schädigung in CFK mittels Akustischer Doppelbrechung. In: . 24. Stuttgarter Kunststoffkolloquium. Stuttgart, Februar.
- Adebahr, W., M. Rahammer, Ronny Sachse, S. Gröninger, M. Käß, Marc Kreutzbruck und G. Busse. 2015. Crack growth monitoring at CFK adhesive bondings. In: . 24. Stuttgarter Kunststoffkolloquium. Stuttgart, Februar.
- Fuhr, Jan-Philipp und Peter Middendorf. 2015. From draping to fracture - Tool chain validation for ply-based composite structures. In: . Composites Virtual Prototyping Expert Seminar. Stuttgart, Januar.
- Middendorf, Peter, T. Sommer-Dittrich, Patrick Böhler, Jörg Dittmann, D. Michaelis, Frieder Heieck und Stefan Zuleger. 2015. Forschungscampus ARENA2036 - Leichtbau durch Funktionsintegration und Aufbau einer digitalen Prozesskette. In: . ATZ Tagung. Stuttgart.
- Dittmann, Jörg. 2015. Permeabilitätsbestimmung und der Weg zu aussagekräftigen Füllsimulationen. In: . AFBW AG Simulation. Fellbach.
- Dittmann, Jörg, Patrick Böhler, D. Michaelis, M. Vinot, C. Liebold, Florian Fritz, H. Finckh und Peter Middendorf. 2015. DigitPro - Digital Prototype Build-up Using the Example of a Braided Structure. In: . 2. International Merge Technologies Conference. Chemnitz.
2014
- Kärger, Luise, Patrick Böhler, Dino Magagnato, S. Galkin und Frank Henning. 2014. Virtuelle Prozesskette für Bauteile aus Hochleistungsfaserverbund. In: . FCC2014. Augsburg, November.
- Fuhr, Jan-Philipp, Patrick Böhler, Frieder Heieck, A. Miene und Peter Middendorf. 2014. Optische Preformanalyse zur 3D-Validierung der Drapier- und Flechtsimulation. In: . FCC2014. Augsburg, November.
- Fuhr, Jan-Philipp, N. Feindler und Peter Middendorf. 2014. Virtuelle Bewertung von Drapiereinflüssen auf die Steifigkeit und Festigkeit von schichtbasierten Faserverbundstrukturen. In: . NAFEMS Seminar. Leipzig, Oktober.
- Kärger, Luise, Florian Fritz, Dino Magagnato, S. Galkin, Alexander Schön, André Oeckerath, K. Wolf und Frank Henning. 2014. Development Stage and Application of a Virtual Process Chain for RTM Components. In: . Proceedings NAFEMS Seminar Simulation of Composites A Closed Process Chain. Leipzig, Oktober.
- Priess, Torben und Peter Middendorf. 2014. Thermische Eigenschaften von Kohlenstoffasern im Hochtemperaturbereich. In: . 4. CFK-Workshop am Institut für Strahlwerkzeuge (IFSW). Stuttgart, Juli.
- Heieck, Frieder. 2014. Klein, groß, günstig, schnell - Textilbasierter Faserverbund-Leichtbau für die Serie. In: . Industrial Composites Production Conference (AUTOMATICA). Augsburg, Juli.
- Dittmann, Jörg. 2014. Permeability determination of resistive welded carbon fabrics. In: . FPCM. Enschede, Juli.
- Middendorf, Peter. 2014. ARENA2036 - Lightweight design and flexible production for next generation automobiles. In: . ICPC Konferenz. Munich, Juni.
- Carosella, Stefan. 2014. Tailored Fibre Placement - a look on its benchmarks. In: . ICS America. Atlanta, USA, Mai.
- Härtel, Frank, Patrick Böhler und Peter Middendorf. 2014. An Integral Mesoscopic Material Characterization Approach. In: . ESAFORM2014. Helsinki, Mai.
- Heieck, Frieder und Jan-Philipp Fuhr. 2014. Wann ist eine Preform ‚gut‘? Qualitätsbestimmung mit optischer Texturanalyse. In: . 1. Technologietag Hybrider Leichtbau. Stuttgart, Mai.
- Böhler, Patrick, Stefan Carosella, C. Götz und Peter Middendorf. 2014. Path definition for tailored fiber placement structures using numerical reverse draping approach. In: . ESAFORM2015. Graz, Austria, April.
- Fuhr, Jan-Philipp, J. Baumann, Frank Härtel, N. Feindler und Peter Middendorf. 2014. Effects of in-plane waviness on the properties of carbon composites - experimental and numerical analysis. In: . 6th International Conference on Composites Testing and Model Identification. Aalborg, Denmark, April.
- Metzner, Christian, A. Gessler, Christian Weimer, U. Beier und Peter Middendorf. 2014. Performance assessments on unidirectional braided CFRP materials. In: . SEICO14. Paris, France, März.
- Priess, Torben, V. Onuseit, Martin Wiedemann, C. Freitag, R. Weber, Peter Middendorf und T. Graf. 2014. Produktive Laserbearbeitung von CFK - der Laser als Werkzeug. In: . SAMPESymposium Deutschland 2014. Stuttgart, Februar.
- Fuhr, Jan-Philipp, N. Feindler und Peter Middendorf. 2014. Berücksichtigung von Fertigungseinflüssen in der Strukturauslegung von schichtbasierten Faserverbundwerkstoffen. In: . SAMPESymposium Deutschland 2014. Stuttgart, Februar.
- Böhler, Patrick, Frank Härtel und Peter Middendorf. 2014. Mesoskopisches Drapieren: Simulation und Validierung. In: . SAMPESymposium Deutschland 2014. Stuttgart, Februar.
2013
- Middendorf, Peter und Klaus Drechsler. 2013. Networks and Private Public Partnerships for R&D on Automotive Composites. In: . IQPC Automotive Composites. Köln, Dezember.
- Böhler, Patrick, Frank Härtel, A. K. Pickett und Peter Middendorf. 2013. Mesoskopischer Ansatz für die Drapiersimulation von unidirektionalen vernähten Textilien. In: . ESI DACH Forum. Wiesbaden, November.
- Böhler, Patrick, Frank Härtel und Peter Middendorf. 2013. Drapieren: Simulation und Verifikation. In: . CCeV. Meitingen, Oktober.
- Middendorf, Peter. 2013. Manufacturing technologies for load-path oriented design: An overview. In: . JEC Americas. Boston, USA, Oktober.
- Priess, Torben und Peter Middendorf. 2013. Gemeinsamkeiten von lasergeschnittenen Kohlenstofffasern und Wattestäbchen. In: . 3. CFK-Workshop am Institut für Strahlwerkzeuge. Stuttgart, Juli.
- Bender, B., Peter Middendorf, Ehard und Milosev. 2013. Stoffschlüssiges Fügen von Aluminium und CFK durch die Epoxidharz-Matrix für die Herstellung hybrider Strukturbauteile. In: . 19. Symposium Verbundwerkstoffe und Werkstoffverbund. Karlsruhe, Juli.
- Middendorf, Peter und Popp. 2013. Advances in Composite Repair. In: . JEC Asia. Singapore, Juni.
- Carosella, Stefan. 2013. Lastpfadgerechte Auslegung und Fertigungsverfahren für Faserkunststoffverbunde. In: . Sika-Technologieforum. Ingolstadt, Mai.
- Carosella, Stefan und Peter Middendorf. 2013. Der Weg zum FVK mit Hilfe direkter Preformverfahren. In: . 23. Stuttgarter Kunststoff-Kolloquium. Stuttgart, März.
- Middendorf, Peter. 2013. Potenzial und Einsatzgebiete von FKV für Leichtbauanwendungen. In: . 23. Stuttgarter Kunststoff Kolloquium. Stuttgart, März.
- Heieck, Frieder. 2013. Entwicklung eines Handhabungsgerätes in Faserverbundbauweise. In: . 2. Augsburger Technologietransfer-Kongress. Augsburg, März.
- Sirtautas, Justas und A. K. Pickett. 2013. Fabric permeability testing and their use in infusion simulation. In: . CompTest. Aalborg.
- Pickett, A. K., Justas Sirtautas und Masseria. 2013. Challenges of VARI process simulation: materials testing and simulation approaches. In: . CCeV. Augsburg.
- Pickett, A. K., Justas Sirtautas und Masseria. 2013. Resin infusion simulation for large structural composite parts. In: . TexComp-11. Leuven.
- Härtel, Frank, Patrick Böhler und Peter Middendorf. 2013. Identification of forming limits for unidirectional carbon textiles in reality and mesoscopic simulation. In: . ESAForm. Aveiro.
- Gnädinger, Florian, Peter Middendorf, Michael Karcher und Frank Henning. 2013. Holistic Design Process for Hollow Structures based on Braided Textiles and RTM. In: . ICCST-9. Sorrento.
- Härtel, Frank und Peter Middendorf. 2013. Process parameter studies and comparison of different preform processes with NCF material. In: . ICCM 19. Montreal.
- Galappathithi, U.I.K., A. K. Pickett, Milos Draskovic, Marc Capellaro und De Silva. A. K. M. 2013. The Effect of Ply Waviness for the Fatigue Life of Composite Wind Turbine Blades. In: . ICREPQ 13 (RE&PQJ). Bilbao.
- Draskovic, Milos, U.I.K. Galappathithi, A. K. Pickett, Marc Capellaro und Peter Middendorf. 2013. Influence of ply waviness on residual strength and fatigue degradation of composite wind turbine blades. In: . ICCM19. Montreal.
- Böhler, Patrick, D. Michaelis, Frieder Heieck und Peter Middendorf. 2013. Numerical prediction and experimental validation of triaxially braided fibre architecture on curved mandrels. In: . TexComp-11. Leuven.
- Pickett, A. K., Justas Sirtautas und Masseria. 2013. Process and challenges for resin infusion simulation of large structural composite parts. In: . CCeV. Stuttgart.
- Kilchert, Sebastian, May, Florian Gnädinger, Michael Karcher und Schoepfer. 2013. Einfluss des Flechtwinkels auf die Werkstoffeigenschaften von Tri-Axialen Geflechten. In: . 19. Symposium Verbundwerkstoffe und Werkstoffverbunde. Karlsruhe.
- Bulat, Martina, Wascinski, Peter Middendorf und Rödel. 2013. Consolidation of braid-based CFRP structures using an expandable mandrel. In: . ICCM. Montreal.
- Gnädinger, Florian, Peter Middendorf, Michael Karcher, Chaudhari und Frank Henning. 2013. Realisierung und Potential von Hohlstrukturbauteilen mit Hinterschnitt im RTM-Verfahren für die automobile Großserie. In: . 19. Symposium Verbundwerkstoffe und Werkstoffverbunde. Karlsruhe.
2012
- Erber, Andreas, Peter Middendorf und Klaus Drechsler. 2012. Automated Process Chains for Carbon Composites. In: . JEC Americas. Boston, November.
- Liebau, van Campen, T. Sommer-Dittrich und Peter Middendorf. 2012. On the Effect of Draping Strategy on FE-Based Draping Simulation of Basic and Complex 3D Geometries for Automated Preforming. In: . 3rd Aircraft Structural Design Conference. Delft, Oktober.
- Middendorf, Peter. 2012. Research: Technology Trends in Composite Simulation. In: . Composite Technologies Symposium. Singapore, September.
- Liebau, van Campen, T. Sommer-Dittrich, Dölle und Peter Middendorf. 2012. An Approach for Investigating the complexity of an Automated Draping Process Using the Finite-Element Method. In: . European Congress on Computational Methods in Applied Sciences and Engineering (ECCOMAS 2012). Wien, September.
- Prieß und Peter Middendorf. 2012. Einfluss des Laserprozesses auf die Faser-Matrix-Anbindung beim Schneiden von Kohlenstofffasern. In: . 2. CFK-Workshop am Institut für Strahlwerkzeuge. Stuttgart, Juli.
- Carosella, Stefan. 2012. Textile Preforming and its potential for automatisation. In: . IQPC Composite Manufacturing. Frankfurt, Juli.
- Prieß, Hafner, Weber, Graf und Peter Middendorf. 2012. Influence of laser processing on carbon fibres. In: . Stuttgart Laser Technology (SLT) Forum. Stuttgart, Juni.
- Middendorf, Peter, Sebastian Jäger und Prowe. 2012. Damage Tolerance of CFRP Airframe Structures: Criteria and Concepts. In: . DLR Bauweisen Kolloquium. Stuttgart, Juni.
- Carosella, Stefan. 2012. Tailored Fibre Placement - an option for automated high volume Preform Production. In: . Sampe Conference SEMAT. Munich, Mai.
- Carosella, Stefan und Marco Hoffmann. 2012. Tailored Fibre Placement - Fasern strukturgerecht ablegen. In: . 13. Textiltechnik Tagung. Chemnitz, März.
- Carosella, Stefan. 2012. Tailored Fibre Placement - Merging stitching and fibre placement technologies. In: . ICS Europe. Paris, März.
- Middendorf, Peter und Karin Birkefeld. 2012. Entwicklungstrends in der Faserverbund-Simulation. In: . Fachkongress Composite Simulation. Fellbach, Februar.
- Carosella, Stefan und Marco Hoffmann. 2012. Das Tailored Fibre Placement Verfahren im Fokus des konstruktiven Leichtbaus. In: . automobil bw: TecNet Gruppe Leichtbau. Esslingen, Januar.
- Bulat, Martina, R. Kehrle, Klaus Drechsler und Bommes. 2012. Effects of pressurized cores on the properties of braided CFRP structures. In: . SAMPE EUROPE 33rd. Paris.
- von Reden, Tjark, Karin Birkefeld, Vigoureux, Blanchard, Henke und Baumgart. 2012. Development of an UD-Braided Longeron With Variable Cross Sections. In: . SAMPE EUROPE 33rd. Paris.
- Liebau, van Campen, T. Sommer-Dittrich und Peter Middendorf. 2012. User- and Process-Defined Benchmark of Kinematic and FE-Draping Codes and Integration into the CAx Process Chain. In: . NAFEMS European Conference Multiphysics Simulation. Frankfurt.
- Erber, Andreas und Klaus Drechsler. 2012. Damage Tolerant Drive Shafts with Integrated CFRP Flanges. In: . SAMPE. Seattle.
- Baumann, J., Frank Härtel, Peter Middendorf, Milwich, Kolja Müller und Planck. 2012. Experimental Draping Studies Based on Standard Textile Testing. In: . Annual World Conference on Carbon 2012. Krakow.
- Gnädinger, Florian, Frank Härtel, Peter Middendorf, Kuhlmann und Bauernhansl. 2012. Design of multifunctional automotive structures using braiding technology. In: . Annual World Conference on Carbon. Krakow.
- Breede, Frieß, Jemmali, Koch, H. Voggenreiter und Frenzel. 2012. Mechanical and microstructural characterization of C/C-SIC manufactured via triaxial and biaxial braided fiber preforms. In: . International conference and Expo on advanced ceramics and composites. Daytona Beach.
- Böhler, Patrick, Bouc, Holger Ahlborn und Peter Middendorf. 2012. Innovative joining of aircraft profiles with braided holes. In: . ECCM 15. Venedig.
- Dransfeld, Siegfried, Karin Birkefeld und Tjark von Reden. 2012. FX-CORE: Functional braiding mandrel for the compression resin transfer moulding of profiles. In: . SAMPE EUROPE 33rd. Paris.
- Hafner, Weber, Graf und Peter Middendorf. 2012. Influence of laser processing on carbon fibres. In: . Laser Technology (SLT) Forum. Stuttgart.
- Härtel, Frank und Peter Middendorf. 2012. A multi-functional Test Rig. In: . Aachen Dresdner Textiltagung. Dresden.
- Dransfeld, Siegfried, Karin Birkefeld und Tjark von Reden. 2012. FX-Core: Functional braiding mandrel for the fast impregnation of hollow profiles. In: . SAMPE Europe Conference SEICO. Paris.
- Härtel, Frank, Wagner, Peter Middendorf und Fleischer. 2012. Draping Strategies and Automation solutions for complex CFRP-Components. In: . SETEC. Lucerne.
- Middendorf, Peter, Andreas Erber und Stefan Carosella. 2012. Flechttechnologie für composite Leichtbaustrukturen: auf dem Weg zur Serienfertigung. In: . Fertigungstechnisches Kolloquium. Stuttgart.
2011
- Carosella, Stefan, Karin Birkefeld und Tjark von Reden. 2011. Entwicklung bis zur Serienumsetzung eines Handhabungsgerätes in Faserverbundbauweise. In: . Materialica Kongress. München, Oktober.
- Carosella, Stefan. 2011. Grundlagen der CFK-Herstellung. In: . 1. Fachtagung CFK Bearbeitung. Stuttgart, Oktober.
- Prieß. 2011. Injektions- und Infiltrationstechnologien für Faserverbundstrukturen. In: . 1. CFK-Workshop am Institut für Strahlwerkzeuge (IFSW). Stuttgart, September.
- Feindler, N., Klaus Drechsler und J. Döll. 2011. Test method to analyse the energy absorption of composite material using flat coupon testing. In: . 5th International Conference on Composites Testing and Model Simulation. Lausanne.
- Pickett, A. K. und Karin Birkefeld. 2011. Analysis and process simulation of textile structures. In: . SAMPE Technical Conference. Zürich.
- Kaiser, Christian Weimer und Klaus Drechsler. 2011. Automated impregnation of preforms for cost-effective manufacturing of fibre reinforced plastics. In: . CFK-Convention. Stade.
- Drechsler, Klaus. 2011. Automatisierte textile Vorformlingtechnologie. In: . Cluster-Treff. Industrielle Prozesskette Hochdruck-RTM bei der KraussMaffei Technologies GmbH.
- Nogueira, Klaus Drechsler, Hombergsmeier und Pacchione. 2011. Investigation of a hybrid 3d-reinforced joining technology for lightweight structures. In: . 16th International Conference on Composite Structures (ICCS 16). Porto.
- Fischer und Klaus Drechsler. 2011. Aluminium Faltkerne für den Einsatz in Sandwichstrukturen. In: . Landshuter Leichtbau-Colloquium. Landshut.
- Mildner, Dölle, Klaus Drechsler und Bjekovic. 2011. Influence of reinforced metal structures using fibre reinforced plastics. In: . SAMPE EUROPE 32nd International Technical Conference. Paris.
- Nogueira, Klaus Drechsler, Hombergsmeier und Pacchione. 2011. Investigation of the properties and failure mechanismus of a damage tolerant 3d-reinforced joint for lightweight structures. In: . Sampe Setec 11. Leiden.
- Werchner, Havar und Klaus Drechsler. 2011. Influence of design and loading on the mechanical behaviour of thick composite lugs. In: . DGLR Kongress. Bremen.
- Erber, Andreas. 2011. Cost Efficient Manufacturing Process of CFRP Truck Side Member. In: . SAMPE EUROPE 32nd International Technical Conference. Paris.
- Seeger, Reese, Jonke, Englhart und Klaus Drechsler. 2011. Cost effective manufacturing of molds for CFRP component production. In: . International Thermal Spray Conference (ITSC). Hamburg.
2010
- Carosella, Stefan. 2010. Tailored Fibre Placement - Über- und Ausblick auf eine prosperierende Textiltechnologie. In: . Fachtagung Technisches Sticken- zwischen Forschung und Markt. Plauen, September.
- Härtel, Frank, Andreas Erber, Klaus Drechsler, Lengowski, Beyermann und Röser. 2010. Development and testing of a lightweight CFRP KA-Band antenna for space applications. In: . JEC. Paris.
- von Reden, Tjark, Martina Bulat und Klaus Drechsler. 2010. Mechanical Performance of Hybrid Carbon Glass Fibre Braids with a High Ratio of 0°-Fibres. In: . 10 TexComp Conference.
- Erber, Andreas, Martina Bulat, Köber, Ménager und Klaus Drechsler. 2010. Development and Test of CFRP Secondary Structures Manufactured by Innovative Textile Preforming Technologies. In: . 31. SAMPE Europe Conference. Paris.
- Drechsler, Klaus. 2010. Carbon Composites in Süddeutschland - Eine Region entwickelt sich zum europäischen High-tech-Standort. In: . 9. Innovation Panel. Meitingen.
- Kehrle, R. 2010. Leichtbauplatten mit Foldcore Kernen. In: . Möbelleichtbau-Symposium. Lemgo.
- Werchner, Havar und Klaus Drechsler. 2010. Design Guidelines and Analysis Methods for Composite Load Introduction Structures. In: . Simulia Konferenz. Heidelberg.
- Kehrle, R. 2010. Leichtbausandwichwerkstoffe. In: . Yachtbau Symposium. Hamburg.
- von Reden, Tjark, Becker und Klaus Drechsler. 2010. Design and Energy Transmission for an Electronic Controlled Lace Bobbin. In: . SETEC 10. Brindisi.
- Clairmont, Klaus Drechsler, Andreas Erber und Frank Härtel. 2010. Automated handling of dry carbon and prepreg materials for the serial production for aeronautical and automotive applications. In: . SAMPE Europe SEMAT. München.
- Drechsler, Klaus. 2010. Was kann man von anderen Märkten lernen? In: . CCeV Automotive Forum. Nackarsulm.
- Kehrle, R. 2010. Forschung und Entwicklung von Faserverbund- und Sandwichleichtbau im Flugzeug- und Automobilbau. In: . VDI Stuttgart. Germany.
- Drechsler, Klaus. 2010. CFK - der Automobilwerkstoff der Zukunft? In: . Internationaler VDI-Kongress Kunststoffe im Automobilbau. Stuttgart.
- Härtel, Frank, Andreas Erber und Klaus Drechsler. 2010. Development and Testing of a Lightweight CFRP Ka-Band Antenna for Space Applications. In: . SAMPE. Paris.
- Erber, Andreas, Weng und Klaus Drechsler. 2010. Effect of Designed Yarn Damages on the Out-of-Plane Properties of Braided Composite Parts. In: . 10 TexComp Conference.
2009
- Kehrle, R. 2009. Chancen durch Faserverbundwersktoffe im Anlagenbau - Potenziale und Risiken. In: . CCe.V. Augsburg. Germany.
- Kehrle, R. 2009. Sandwichbauweisen in der Luftfahrt. In: . Leichtbaukolloquium. Landshut.
- Grave, Karin Birkefeld, Tjark von Reden, Klaus Drechsler, Yordan Kyosev und Rathjens. 2009. Simulation of 3D overbraiding - Solutions and Challenges. In: . Second World Conference on 3D Fabrics and their Applications. Greenville.
- Erber, Andreas, Karin Birkefeld und Klaus Drechsler. 2009. The Influence of Braiding Configuration on Damage Tolerance of Drive Shafts. 30. In: . SAMPE Europe Conference. Paris.
- Kehrle, R. 2009. Faserverbundwerkstoffe. In: . IHK. Reutlingen.
- Johnson, Alastair, Sebastian Kilchert, Fischer und R. Kehrle. 2009. New structural composite core materials. In: . Composites. Gold Coast.
- Erber, Andreas, Beyersdorff und Klaus Drechsler. 2009. Neue Gesamtkonzepte und Fertigungstechnologien für FVK-Druckwalzen. In: . Composites in Automotive and Aerospace Kongress. Materialica.
- Erber, Andreas, Gittel, Geiger, Chaudhari, Frank Henning und Klaus Drechsler. 2009. Advanced Damage Tolerance of CFRP Laminates using In-Situ Polymerised Thermoplastics. In: . SAMPE Europe Technical Conference. Filton.
- George, A., Klaus Drechsler und Holmberg. 2009. The Permeability of Tackified, Stitched, and Braided Carbon Fiber Textiles: Experi-mental Characterization and Design Modeling. In: . SAMPE. Baltimore.
- George, A., Klaus Drechsler und Holmberg. 2009. The Permeability of Carbon Fiber Preforming Materials: Sensitivity to Fabric Geometry. In: . 20th Annual International SICOMP Conference. Pite\aa.
2008
- Carosella, Stefan. 2008. The Forefront of Textile Composite Research in Europe. In: . Aerospace Industrial Technology Show. Nagoya.
- Erber, Andreas. 2008. Flechttechnologie - Kostenoptimiertes Fertigungsverfahren für Faserverbundbauteile. In: . CFK-Technologietag. Hamburg.
- Carosella, Stefan. 2008. Sticken ein textiles Preformverfahren. In: . 2. CFK Technologietag Airbus. Hamburg.
- Kunze, C. Wellhausen, Leistner, Demel, Roser und Klaus Drechsler. 2008. Entwicklung von Faserverbund-Hohlbauteilen in RTM-Bauweise am Beispiel eines Traglenkers von Passagierflugzeugtüren. In: . Proc. Deutscher Luft- und Raumfahrtkongress. Darmstadt.
- Wagner, Bansemir und Klaus Drechsler. 2008. Verhalten unterschiedlicher FVW-Bauweisen und Fertigungstechniken unter Schlagbelastung. In: . Deutscher Luft- und Raumfahrtkongress. Darmstadt.
- Bulat, Martina. 2008. Textile technology as an innovative manufacturing method for highperformance fibre composite structures. In: . 4th International Textile. Dubrovnik.
2007
- Kaiser, Garschke, Bronwyn Fox, Christian Weimer und Klaus Drechsler. 2007. Out of Autoclave Manufacture of Structural Aerospace Composite Materials. In: . International European SAMPE Conference. Paris.
- Breckweg, Meyer, Klaus Drechsler und Rüger. 2007. Fast and Intuitive Robot Programming for Mandrel Guiding of Braiding Machines for Textile Preforming. In: . International European SAMPE Conference. Paris.
- Drechsler, Klaus und Friedrich. 2007. Wege zur kostengünstigen Fertigung von Hochleistungsverbundstrukturen in innovativen Fahrzeugkonzepten. In: . Handelsblattsymposium Werkstoffe und Fertigungstechnik, Technologien und Bauweisen. Stuttgart.
- Kümpers, Brockmanns, Klaus Drechsler und Rüger. 2007. Cost Effective Manufacturing of complex textile preforms by automated braiding technologies. In: . International European SAMPE Conference. Paris.
- Wagner, Bansemir, Klaus Drechsler und Christian Weimer. 2007. Impact Behaviour and Residual Strength of Carbon Fiber Textile based Materials. In: . 3rd SAMPE Europe Technical Conference. Madrid.
2006
- Feher, Klaus Drechsler und J. Filsinger. 2006. Development of a Modular 2,45 GHz HEPHAISTOS-CA2 Microwave Processing System for Automated Composites Fabrication. In: . International European SAMPE Conference. Paris.
- Drechsler, Klaus, Herkt, Less und Riegel M. 2006. Dynamic testing of 3D-reinforced composite T-joints. In: . ICAS. Hamburg.
- Aoki, Kensche, Eberle, Wagner, T. Keilig und Klaus Drechsler. 2006. NDE Assessment of Long Fibre Reinforced GFRP and CFRP. In: . Conference on Damage and its evolution in fibre composite materials. Stuttgart.
- Drechsler, Klaus und Ingo Karb. 2006. Design and Performance of Composite Structures made by Tailored Fibre Placement Technology. In: . SAMPE International Conference. Long Beach.
- Drechsler, Klaus, Schouten und Havar. 2006. 3D reinforcement improving interlaminar shear and peel strength for composites loops. In: . International European SAMPE Conference. Paris.
- Pfleiderer, Wagner, Klaus Drechsler und G. Busse. 2006. Application and potential of emerging NDE-methods for carbon fibre reinforced composites. In: . Proceedings 27th Sampe Europe Conference. Paris.
- Drechsler, Klaus, Herkt, Peter Middendorf, Less und Riegel M. 2006. 3D-reinforcement of composite T-joints by means of robot assisted stitching technologies. In: . SAMPE International. Long Beach.
- Palacin und Klaus Drechsler. 2006. The Marie Curie Program Momentum - Composites in Transport. In: . International European SAMPE Conference. Paris.
- Drechsler, Klaus, R. Kehrle, Yves Klett und E. Thorsteinsson. 2006. Faltwabenkerne für multifunktionale Leichtbaustrukturen. In: . 2nd MATERIALICA Composites Congress Composites in Automotive Aerospace. München.
- Drechsler, Klaus und Wagner. 2006. Fatigue Behavior and Residual Strength of Textile Based Materials. In: . Conference on Damage and its evolution in fibre composite materials. Stuttgart.
- Drechsler, Klaus. 2006. Chancen für CFK im Automobil- und Flugzeugbau durch integrierte Fertigungstechnik. In: . Bayern Innovativ Symposium Polymere im Automobilbau. München.
- Weis, Hoflin, Deimel, Bilgram und Klaus Drechsler. 2006. Damage Detection Using Fibre Bragg Grating Sensors. In: . Proceedings of the European Conference on Non Destructive Testing. Berlin.
2005
- Havar und Klaus Drechsler. 2005. 3D Fibre Reinforcement improving interlaminar shear and peel strength of composite loops. In: . SAMPE. Paris.
- Drechsler, Klaus. 2005. Neueste Entwicklungen der Faserverbundtechnologie für den Flugzeug- und Automobilbau. In: . Vortrag VDI Arbeitskreis Produktionstechnik. Stuttgart.
- Drechsler, Klaus und A. Gessler. 2005. Textile Fertigungsverfahren für optimierte Faserverbundstrukturen. In: . WING-Konferenz. Aachen.
- Kehrle, R. und Pfaff. 2005. Mechanische Eigenschaften neuartiger Sandwichkerne. In: . 6. Nationales Symposium SAMPE. Stuttgart.
- Kehrle, R. und Klaus Drechsler. 2005. Manufacturing and performance of folded honeycomb structures. In: . SAMPE. Long Beach.
- Kehrle, R. und Klaus Drechsler. 2005. Manufacturing, Simulation and performance of sandwich structures with folded core. In: . 25th International SAMPE Conference. Paris.
- Drechsler, Klaus und T. Keilig. 2005. Schädigungscharakterisierung an NCF-Laminaten mittels Lockin-Thermographie und Bestimmung der CAI-Restfestigkeiten. In: . 1.Kunststoffkolloqium. Stuttgart.
Bereichsleitung
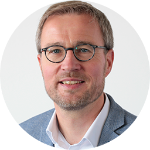
Peter Middendorf
Prof. Dr.-Ing.Leiter Bereiche Leichtbau/Simulation und Fertigungstechnologie

Stefan Carosella
Dr.-Ing.Stellvertretender Leiter Bereich Fertigungstechnologie