Die Simulation von Infusionsprozessen ist mitunter sehr komplex und in den meisten Fällen reicht es nicht aus, den Eingangs-/Ausgangsdruckgradienten, die Harzviskosität und die Permeabilität des Faserhalbzeugs zu definieren. In der Realität beeinflusst eine Vielzahl von mikroskopischen, mesoskopischen und makroskopischen Effekten die Fließfront des Harzes durch die Faserverstärkung. Auswirkungen, zum Beispiel die lokale Verdichtung und Scherung des trockenen Faserhalbzeugs, können aus einer Vielzahl von Gründen wie Werkzeugkomplexität, Radien und variablen Abschnitten hervorgerufen werden und zu inhomogenen Füllungen oder Abweichungen vom geplanten Fließweg führen. Andere Effekte, z.B. Schnellläufer, sind noch komplexer und unvorhersehbarer und können zu plötzlichen Infusionsänderungen führen, sowohl in Bezug auf die Orientierung als auch auf die Geschwindigkeit. Die Modellierung solcher Effekte ist daher ein großes Forschungsthema am Institut für Flugzeugbau. Die Kombination all dieser Techniken wird außerdem zur Simulation von Defekten wie Porosität und trockenen Stellen eingesetzt.
Weiterführende Informationen und Förderprojekte
Ausgangssituation/Zielsetzung
-
Die intelligente Datensammlung, -aufbereitung und -übergabe über die gesamte Wert-schöpfungskette – von der Idee, über Design, Produktion und In-Service bis hin zum End-of-Life – für das intelligente Bauteil und die wandlungsfähige, autonome Fabrik von Übermorgen. Um dieses Vorhaben realisieren zu können, ist ein durchgängiger Datenfluss zu jedem Zeitpunkt und Prozessschritt notwendig. Kontextbezogene Semantiken werden benötigt, damit die verschiedenen Datentypen jederzeit korrekt zugeordnet werden können. Unterschiedlichste Disziplinen tauschen Daten aus und müssen dabei stets wissen, wo sich die Daten der vorhergehenden Schritte befinden und was sie genau bedeuten.
-
Die Basis hierfür bildet der Digitale Fingerabdruck eines jeden Bauteils, in dem alle Daten vom ersten Konzept, über Konstruktion, Berechnung, Prozessdaten, Maschinendaten, Logistikdaten, bis hin zu In-Service Daten aus integrierten Sensoren hinterlegt und intelligent verknüpft sind. Das Hauptziel des Digitalen Fingerabdrucks ist daher die Weiterentwicklung eines Bauteils zu einer Industrie 4.0-Komponente und die Schaffung der notwendigen Basis für die intelligente Wertschöpfungskette eines Bauteils für die Zukunft.
-
Der digitale Fingerabdruck kann somit auch als Basis für Industrie 4.0-Anwendungen und dementsprechend als Bindeglied zwischen allen ARENA2036-Verbundprojekten verstanden werden.
Kontakt
Weiterführender Link
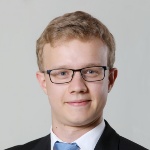
Simon Thissen
M.Sc.Wissenschaftlicher Mitarbeiter