At the Institute of Aircraft Design, methods are being developed for the evaluation of large assemblies with regard to manufacturability in fiber composite construction. Both the manufacturing process, the fiber material or semi-finished product, and the component geometry have an influence on resulting manufacturing effects. The approach is based on the hypothesis: similar geometric challenges produce similar manufacturing effects as long as the process and material remain identical. Systematic storage of component geometries in a database, including the resulting manufacturing effects, enables the derivation of manufacturing effects on newly designed components by comparing the new component geometry with geometries in the database.
Specific geometric features can be defined on the basis of targets. In this case, the targets are specifically manufacturing effects that result from the forming of flat textile semi-finished products. These features can be detected by specially programmed algorithms in common CAD software environments and stored in an HDF5 database. In the analysis, an automated CAD analysis for HDF5 databases of geometric features is performed. This is followed by rapid data matching based on upstream global criteria. To speed up database matching, global features and feature distribution functions of the parts are used first, for example. This results in a filtering of possible similar parts in the database. A detailed comparison of geometries, including freeform surfaces, can be done by translating the geometry into a point cloud. For this purpose, fast algorithms for the generation of adequate point clouds as well as for the geometric comparison of point clouds have to be developed. It should be possible to weight individual geometric criteria according to their influence. Calibration can be performed by real or simulated manufacturing effects.
Additional information and funding projects
Dissertation carried out at the institute on the subject
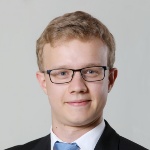
Simon Thissen
M.Sc.Research Associate